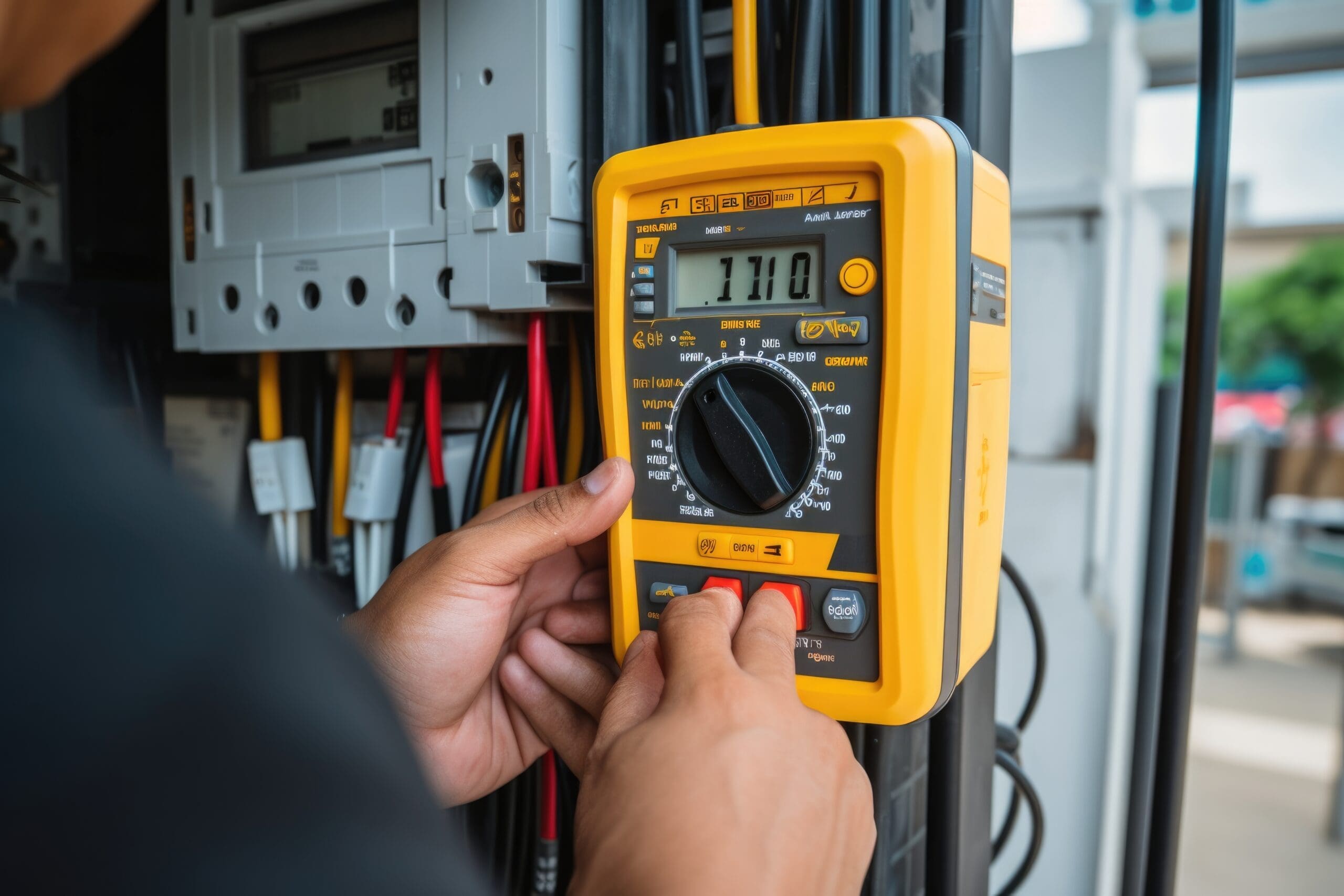
In Australia, ensuring electrical safety in workplaces and public spaces is a critical concern. One of the key practices to achieve this is testing and tagging electrical equipment. This process not only complies with national safety regulations but also helps prevent electrical hazards that can lead to accidents, injuries, or even fatalities. Whether you are a business owner, facility manager, or simply interested in electrical safety, this blog will provide you with a comprehensive overview of testing and tagging in Australia.
What is Testing and Tagging?
Testing and tagging is a systematic process that involves inspecting, testing, and labelling electrical equipment to ensure it is safe to use. This process is conducted by qualified technicians who follow specific standards and guidelines. It includes two main components:
- Visual Inspection: Checking the equipment for any visible signs of damage, wear, or defects.
- Electrical Testing: Using specialized equipment to test the functionality and safety of the electrical components.
Once the equipment passes these checks, a tag is attached indicating the date of testing, the next due date, and the technician’s details.
Why is Testing and Tagging Important?
Testing and tagging are crucial for several reasons:
- Safety Compliance: Adhering to national and state regulations, such as the Work Health and Safety (WHS) Act, which mandate regular testing and tagging of electrical equipment in workplaces.
- Preventing Accidents: Identifying and mitigating potential electrical hazards that could lead to shocks, fires, or other accidents.
- Insurance Requirements: Many insurance policies require proof of regular testing and tagging to cover claims related to electrical incidents.
- Maintenance: Proactively maintaining equipment to extend its lifespan and ensure it operates efficiently.
Legal Requirements and Standards
In Australia, testing and tagging practices are governed by several standards and regulations:
- AS/NZS 3760: This standard provides the guidelines for in-service safety inspection and testing of electrical equipment. It outlines the frequency of testing and the procedures to be followed.
- Work Health and Safety (WHS) Regulations: These regulations require employers to ensure the electrical safety of their workplaces, which includes regular testing and tagging.
- State-Specific Regulations: Different states and territories may have additional requirements and guidelines for testing and tagging.
Who Needs to Test and Tag?
Testing and tagging are essential for various environments and industries, including:
- Offices: Ensuring that computers, printers, and other office equipment are safe.
- Construction Sites: Regularly checking power tools, extension cords, and other site equipment.
- Factories and Warehouses: Testing machinery, conveyors, and other heavy equipment.
- Schools and Universities: Ensuring the safety of electrical devices used by staff and students.
- Hospitals and Clinics: Regularly testing medical equipment and devices.
Frequency of Testing and Tagging
The frequency of testing and tagging depends on the type of equipment and the environment in which it is used. According to AS/NZS 3760, some general guidelines include:
- Construction Sites: Every 3 months
- Factories and Workshops: Every 6 months
- Offices: Every 12 months
- Hostile Environments: Every 6 months (environments where the equipment is exposed to conditions that could cause damage, such as moisture, heat, or chemicals)
The Testing and Tagging Process
The testing and tagging process involves several steps:
- Visual Inspection: The technician checks for any obvious damage, such as frayed cords, cracked casings, or exposed wires.
- Electrical Testing: Using a Portable Appliance Tester (PAT), the technician conducts a series of tests, including:
- Earth Continuity Test: Ensures the earth wire is properly connected.
- Insulation Resistance Test: Checks the insulation around the wires to prevent short circuits.
- Polarity Test: Ensures the wiring is correctly connected.
- Tagging: If the equipment passes the tests, a tag is attached. If it fails, it is either repaired or taken out of service.
- Documentation: Detailed records are kept, including the test results, the date of testing, and the next due date.
Choosing a Testing and Tagging Service
When selecting a testing and tagging service provider, consider the following:
- Qualifications: Ensure the technicians are qualified and certified to perform testing and tagging.
- Experience: Choose a provider with a proven track record and experience in your specific industry.
- Compliance: Verify that the service adheres to all relevant standards and regulations.
- Reputation: Look for reviews and testimonials from previous clients to gauge the provider’s reliability and quality of service.
Conclusion
Testing and tagging are essential practices to ensure electrical safety in Australia. By adhering to national standards and regulations, businesses can protect their employees, customers, and assets from electrical hazards. Regular testing and tagging not only help maintain a safe working environment but also contribute to the efficient operation and longevity of electrical equipment.
Staying informed and proactive about testing and tagging can make a significant difference in preventing accidents and ensuring compliance. So, prioritize electrical safety, choose a reputable testing and tagging service, and keep your workplace safe and efficient.
Embrace the practice of testing and tagging, and take a step towards a safer, more secure future.